Go No Go Gauge: Your Ultimate Precision Tool
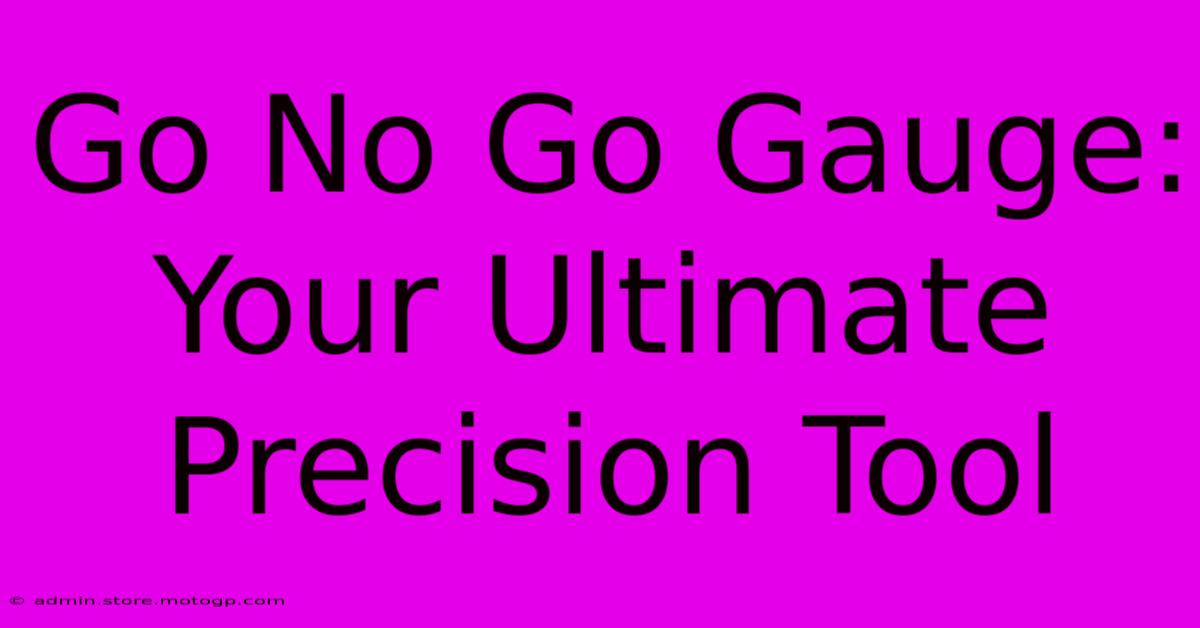
Table of Contents
Go No Go Gauge: Your Ultimate Precision Tool
Go/No-Go gauges are indispensable precision measurement tools used to quickly and easily determine whether a part falls within acceptable tolerance limits. Unlike traditional measuring instruments that provide precise dimensions, Go/No-Go gauges offer a simple pass/fail assessment, making them crucial for quality control and inspection in various manufacturing and engineering sectors. This comprehensive guide will delve into the intricacies of Go/No-Go gauges, explaining their functionality, types, applications, and advantages.
Understanding Go No Go Gauge Functionality
A Go/No-Go gauge set typically consists of two gauges: a "Go" gauge and a "No-Go" gauge. The "Go" gauge represents the maximum acceptable size of a part, while the "No-Go" gauge represents the minimum acceptable size. The principle is straightforward:
- Go Gauge: If the part fits snugly onto the Go gauge, it indicates that the part's size is within the acceptable tolerance range.
- No-Go Gauge: If the part does not fit onto the No-Go gauge, it signifies that the part's size is still within the acceptable tolerance. If it does fit, the part is outside the acceptable tolerance and is considered rejected.
This binary system provides an immediate and unambiguous assessment of part conformity, eliminating the need for complex calculations and reducing the potential for human error.
Types of Go No Go Gauges
Go/No-Go gauges are available in various designs to cater to different applications and measurement needs:
- Cylindrical Plug Gauges: Used for measuring the internal diameter of cylindrical parts, such as holes or bores.
- Cylindrical Ring Gauges: Used for measuring the external diameter of cylindrical parts, such as shafts or pins.
- Thread Gauges: Designed to inspect the accuracy of screw threads, ensuring proper fit and function. These gauges come in "Go" and "No-Go" versions for both internal and external threads.
- Snap Gauges: Feature a spring-loaded mechanism and are often used for rapid and repeated measurements.
- Special Gauges: Custom-designed gauges cater to specialized shapes and dimensions, meeting unique application requirements.
Advantages of Using Go No Go Gauges
The popularity of Go/No-Go gauges stems from numerous advantages:
- Speed and Efficiency: Provides rapid pass/fail determinations, significantly accelerating the inspection process.
- Simplicity: Requires minimal training and expertise to operate effectively, reducing the learning curve.
- Accuracy: Manufactured to precise tolerances, ensuring reliable and consistent measurements.
- Reduced Errors: The binary pass/fail system minimizes the risk of human error associated with subjective interpretations of measurements.
- Cost-Effectiveness: While the initial investment might seem higher than simple measuring tools, the time and resource savings quickly offset the cost, particularly in high-volume production environments.
- Improved Quality Control: Enables immediate identification of non-conforming parts, preventing defective items from entering the final product.
Applications of Go No Go Gauges
Go/No-Go gauges find extensive application across numerous industries:
- Automotive Industry: Ensuring the dimensional accuracy of critical engine components, transmission parts, and body panels.
- Aerospace Industry: Meeting stringent tolerance requirements for aircraft components where precision is paramount.
- Manufacturing: Maintaining consistent quality and dimensional accuracy across various manufacturing processes.
- Machining: Verifying the accuracy of machined parts and ensuring conformity to specifications.
- Medical Device Manufacturing: Meeting strict regulatory requirements for medical devices, guaranteeing patient safety and efficacy.
Choosing the Right Go No Go Gauge
Selecting the appropriate Go/No-Go gauge depends on several factors:
- Part Dimensions: Determine the required size and type of gauge to match the part's dimensions.
- Material: Choose a gauge material that is compatible with the part material to prevent damage or wear.
- Tolerance Requirements: Select a gauge with tolerances that meet the required precision for the application.
- Gauge Type: Choose the appropriate type of gauge, such as cylindrical plug, ring, or thread gauge, depending on the part's shape and features.
Conclusion: The Indispensable Quality Control Tool
Go/No-Go gauges are invaluable tools for maintaining quality control and ensuring dimensional accuracy in diverse industries. Their simplicity, speed, and accuracy contribute to increased efficiency and reduced error rates. By understanding the various types, applications, and advantages of Go/No-Go gauges, manufacturers and engineers can leverage their full potential for optimizing production processes and delivering high-quality products. Investing in the right Go/No-Go gauge is an investment in precision and efficiency.
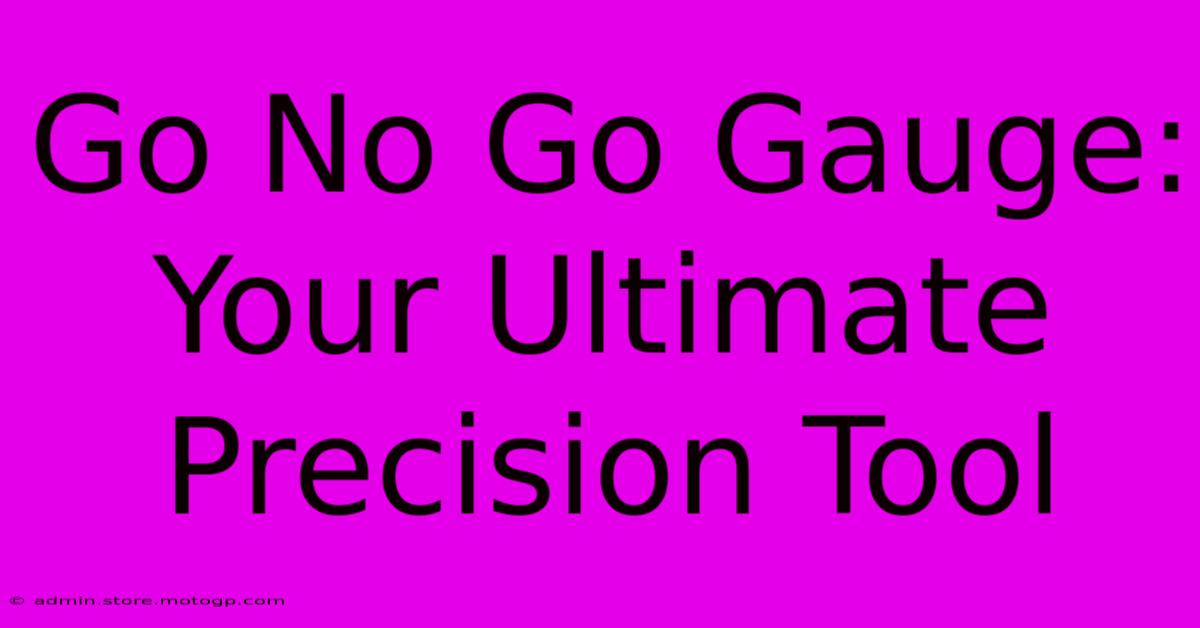
Thank you for visiting our website wich cover about Go No Go Gauge: Your Ultimate Precision Tool. We hope the information provided has been useful to you. Feel free to contact us if you have any questions or need further assistance. See you next time and dont miss to bookmark.
Featured Posts
-
Hadestown Explained Unpacking The Myth And The Musical
Feb 10, 2025
-
Ditch Your Smartphone Capture Breathtaking Images With The Canon Rebel T5
Feb 10, 2025
-
Ohio Governor Race 2024 Whos Vying For Your Vote
Feb 10, 2025
-
Oklahoma Sooners Football Stadium Creating Unforgettable Memories
Feb 10, 2025
-
Push It Real Good Your Guide To Effortless Productivity
Feb 10, 2025