The Future Of Corrosion Control: How New Coatings Are Defying Time
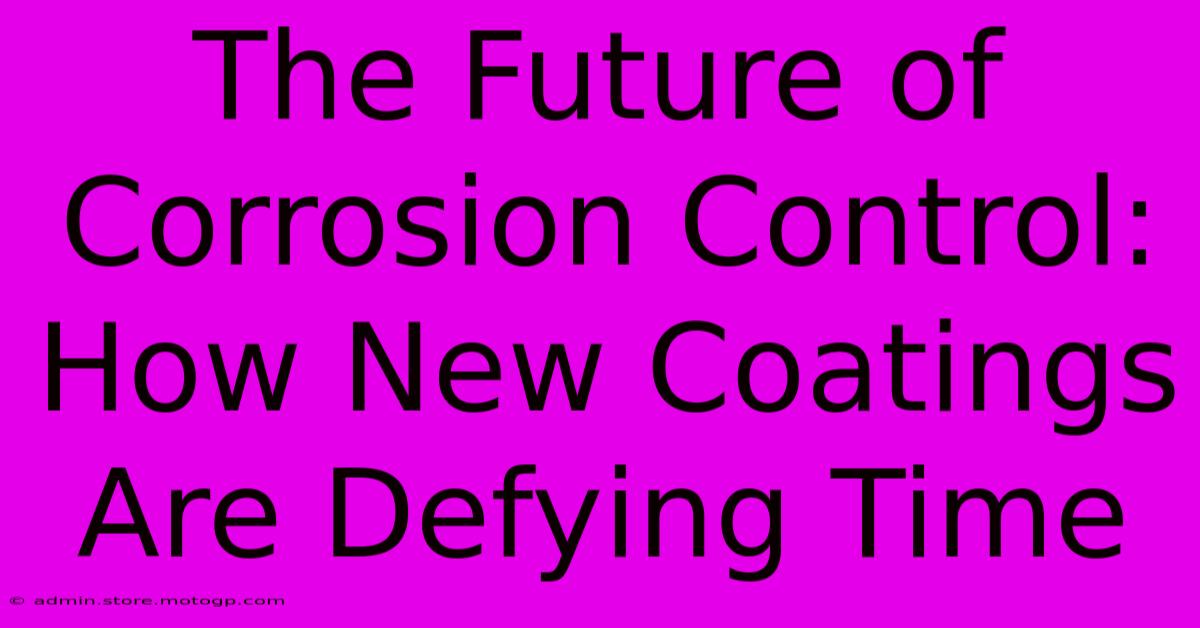
Table of Contents
The Future of Corrosion Control: How New Coatings Are Defying Time
Corrosion—the gradual destruction of materials due to chemical reactions with their environment—is a silent, costly menace impacting infrastructure, industry, and even our everyday lives. From rusting bridges to degrading pipelines, the economic and safety implications are enormous. But the fight against corrosion is evolving, with innovative coatings pushing the boundaries of protection and promising a future where materials endure longer and stronger. This article explores the cutting edge of corrosion control, showcasing how new coatings are defying time.
What are the major challenges in current corrosion control methods?
Traditional corrosion prevention methods, such as galvanization and painting with conventional coatings, often fall short in harsh environments or when long-term protection is crucial. These methods can be labor-intensive, require frequent maintenance and reapplication, and may not provide sufficient protection against aggressive chemicals or extreme temperatures. Furthermore, the environmental impact of some traditional coatings is a growing concern.
How are new coatings improving on traditional methods?
The future of corrosion control hinges on advancements in materials science and nanotechnology. New coatings are being developed with enhanced properties, offering superior protection and longevity compared to their predecessors. These improvements come in several key areas:
Enhanced Barrier Properties:
Many new coatings utilize advanced polymers and nano-composites to create incredibly dense and impermeable barriers. These materials effectively block the ingress of moisture, oxygen, and corrosive agents, significantly slowing down or even halting the corrosion process. Examples include:
- Polymer nano-composites: These coatings incorporate nanoparticles (e.g., silica, alumina) within a polymer matrix, creating a denser and more robust barrier than traditional polymer coatings. The nanoparticles also enhance the mechanical properties, improving scratch and abrasion resistance.
- Self-healing coatings: These innovative coatings contain microcapsules filled with corrosion inhibitors. When the coating is damaged, the capsules break, releasing the inhibitors that repair the damaged area and restore the protective barrier.
Improved Adhesion and Durability:
The effectiveness of any coating relies heavily on its adhesion to the substrate. New coating technologies focus on creating stronger bonds between the coating and the underlying material. Surface treatments, such as plasma spraying or laser ablation, can improve surface roughness and enhance adhesion. Moreover, advanced polymers and modified resin systems provide better flexibility and resistance to cracking, chipping, and peeling.
Enhanced Corrosion Inhibition:
Some new coatings incorporate active corrosion inhibitors directly into their formulation. These inhibitors can chemically react with corrosive agents, neutralizing their effect and preventing corrosion from initiating. Inorganic inhibitors, such as zinc phosphate or chromate-free alternatives, are being integrated into polymeric coatings to provide long-lasting protection.
What are some specific examples of new coatings being used?
The applications of these new coatings span various industries. For example:
- Marine industry: High-performance coatings are used to protect ships' hulls and offshore structures from saltwater corrosion.
- Oil and gas industry: Protective coatings are crucial for pipelines and storage tanks operating in harsh environments.
- Automotive industry: New coatings enhance the durability and appearance of vehicle components.
- Aerospace industry: Corrosion-resistant coatings are vital for protecting aircraft from atmospheric conditions.
What are the environmental benefits of new coatings?
Many traditional coatings contain harmful substances, such as chromates and heavy metals. The development of environmentally friendly coatings represents a significant step forward. New coatings are formulated using less toxic materials, reducing the environmental impact of corrosion control measures. This is crucial for promoting sustainability and responsible industrial practices.
What are the future trends in corrosion control coatings?
The field of corrosion control is constantly evolving, with ongoing research focused on developing even more effective and sustainable coatings. Future trends include:
- Smart coatings: Coatings that incorporate sensors to monitor corrosion in real-time.
- Bio-inspired coatings: Coatings that mimic the self-healing properties of biological systems.
- Multifunctional coatings: Coatings that offer multiple functionalities beyond corrosion protection, such as anti-fouling or self-cleaning properties.
Conclusion
The future of corrosion control looks bright. New coatings are offering unprecedented levels of protection, durability, and sustainability. As research continues and technology advances, we can expect even more sophisticated and effective coatings to emerge, prolonging the lifespan of vital infrastructure and protecting valuable assets for years to come. The fight against corrosion is far from over, but the arsenal of new coating technologies offers a potent and promising path forward.
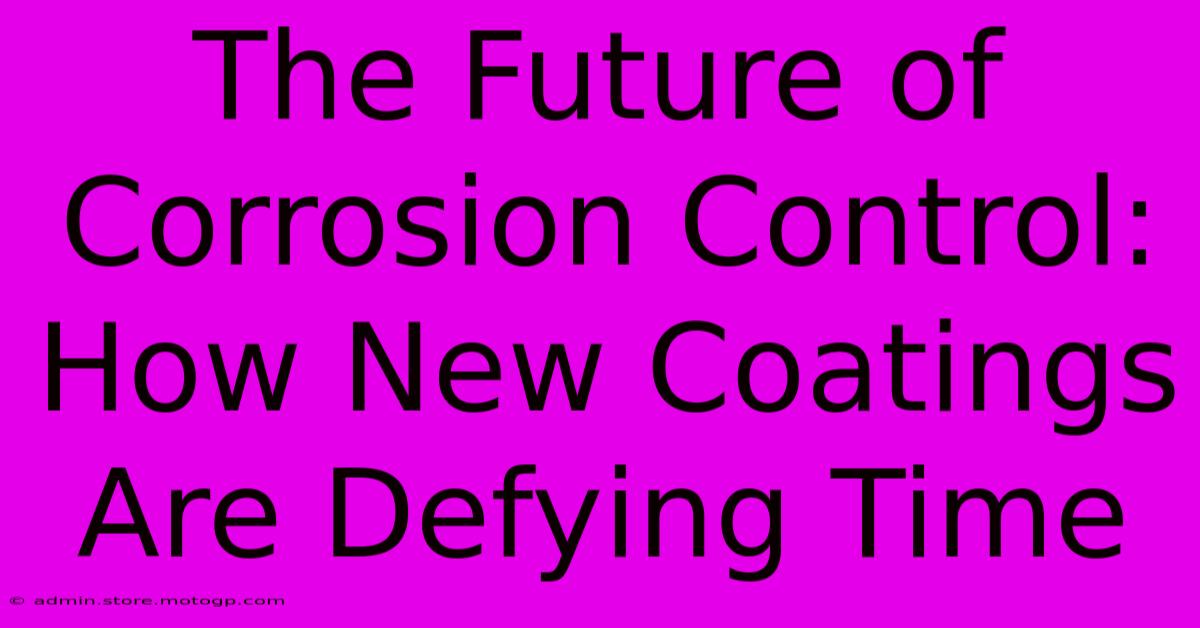
Thank you for visiting our website wich cover about The Future Of Corrosion Control: How New Coatings Are Defying Time. We hope the information provided has been useful to you. Feel free to contact us if you have any questions or need further assistance. See you next time and dont miss to bookmark.
Featured Posts
-
The Key To Eye Catching Content Unlocking The Tetradic Color Code
Mar 21, 2025
-
Discover The Enchanted Collection Disney Products That Will Make Your Dreams Come True
Mar 21, 2025
-
Kiss The Bouquet Away Stunning Valentines Day Floral Masterpieces
Mar 21, 2025
-
Bon Appetit Bonehead Da Meme That Breaks Zaban
Mar 21, 2025
-
Surrender To The Soulful Embrace Of Chapter 8 By Anita Baker The Songs That Will Heal Your Heart
Mar 21, 2025